The Akron-Canton Section (#810) of the American Society For Quality kicked off their fall monthly meeting schedule on September 16, 2010 at the 356th Fighter Group Restaurant in North Canton, Ohio. The featured speaker was John Novak, president of KAVON International, Inc. and a Certified Lean Six Sigma Master Black Belt. John facilitated both the Technical Clinic and the dinner meeting.
Technical Clinic
During the Technical Clinic, John demonstrated the use of Quality Companion (from Minitab) as a tool to manage, track and document continual improvement projects using the DMAIC methodology. He covered the following features:
- Setting up a DMAIC project roadmap
- Creating a custom project roadmap
- Establishing a project charter
- Creating Process Maps
- Creating and modifying an FMEA
- Creating and loading custom templates
- Using Quality Companion coaches
- Using analysis forms to report and interpret results from a Minitab analysis
- Attaching external files to your project
- Creating a presentation
- Exporting project information to PowerPoint
- Importing Visio flowcharts
John also mentioned that a free Quality Companion Viewer can be downloaded from the Minitab website to allow anyone to view the contents of a Quality Companion project file without being able to make changes. He indicated that by placing these project files on a central network location, it would facilitate communication among all employees in an organization by allowing them to view current and completed projects and possibly contribute valuable information.
Lastly, John mentioned that a free Quality Companion Dashboard was also available as a free download from the Minitab website, which allows project managers to view the status of projects together as a group.
Dinner Meeting
During the dinner meeting, John gave a talk on,
"Deploying Lean Six Sigma to meet the Continual Improvement requirements of ISO 9001."
John started out by visiting the following requirements within ISO 9001:
- Quality Policy
- Quality Objectives
- Definition Of Major Processes
- Process Measures
- Continual Improvement
He pointed out how continual improvement was a common theme in all of these requirements. He also commented on the process approach that was introduced in ISO 9001:2000 and gave a description of the components of a process:
- Inputs
- Activities
- Outputs
- Measures of Effectiveness
John introduced a Continual Improvement model, which would meet the requirements of the various Quality Management System standards like ISO 9001.
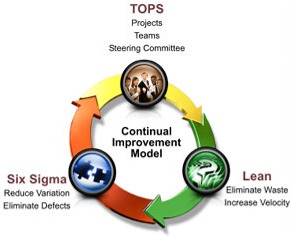
It contained the following components:
- TOPS: Defines the steering committee, which consists of top management individuals. They approve and select projects that contribute to the realization of the organization’s strategic objectives. Once a project is selected, this group builds the team to complete the project.
- Lean: The component of the model that identifies and eliminates the waste in a process. Waste is anything the customer is unwilling to pay for.
- Six Sigma: Looks at the variation in the process and attempts to identify and reduce it, thus reducing defects.
John described the following Lean Six Sigma deployment steps:
- Steering Committee Selects Project
- Steering Committee Assigns The Champion & Team Leader
- Champion & Team Leader Draft & Sign A Project Charter
- Steering Committee Assigns The Project Facilitator (Black Belt)
- Champion & Team Leader Select Other Team Members
- The Team Selects A Recorder
- The Team Reviews The Project Charter
- The Team Organizes A Plan To Proceed
- The Project Is Launched!
John described the members and roles of an effective Continual Improvement team. He described the role that each played and how they complemented each other. The following roles were defined:
- Champion
- Team Leader
- Facilitator
- Recorder
- Cross-Functional Members
Finally, John brought it back to ISO 9001 by describing the following elements of the standard that can be used to sustain the gains achieved by the project team:
- Document Control
- Internal Auditing
- Corrective and Preventive Actions
- Process Measurement
- Management Review
The session concluded with a period of questions and answers.