What is Continual Improvement and how do I satisfy the requirements defined in ISO 9001? This is a question I have been asked numerous times from companies seeking certification to the various quality management system standards like ISO 9001.
Why is Continual Improvement Important to the Organization?
The first thing we have to understand is
"Why" we should do this. The
ISO 9000:2005 standard, Clause 2.9, contains the following definition:
The aim of continual improvement of a quality management system is to increase the probability of enhancing the satisfaction of customers and other interested parties.
Competing in a global marketplace can reduce the probability of enhancing customer satisfaction if we don’t stay one step ahead of our current competitors and any new competitors which may enter our market space. Even if you currently enjoy a dedicated customer base, with few competitors, you can’t count on the status quo forever. New regulations, customer requirements, market mix, technology and a myriad of other changes may blind side you and force you to play catch-up just to survive. The best policy is to be continually improving your processes in order to remain the leader and not the follower.
What are the Requirements?
Now that we have described
"Why" we should engage in continual improvement activities, what are the specific requirements needed for certification? The
ISO 9001:2008
The organization shall continually improve the effectiveness of the quality management system through the use of the quality policy, quality objectives, audit results, analysis of data, corrective and preventive actions and management review.
This requirement starts with the Quality Policy, which must contain a commitment to comply with requirements and to continually improve the effectiveness of the quality management system. Next, the Quality Objectives must support the commitment to continual improvement and be measurable so through the analyzing of company data, you know if you are achieving the objective. The internal auditing process has the requirements of evaluating the progress toward the achievement of the Quality Objectives and the company’s continual improvement efforts. If any deficiencies are identified, they must be documented and action must be taken to correct them through the Corrective and Preventive Action processes. Lastly, the management group of the organization must periodically review the results of the quality management system and take appropriate actions to achieve the Quality Objectives and fulfill the Quality Policy.
The continual improvement efforts must be documented in order to show objective evidence, to the internal and external auditors, that the requirements are being satisfied.
What Constitutes Continual Improvement?
Continual Improvement efforts manifest themselves in many different forms. One manifestation is in the form of large, resource intensive projects, which usually result in a major change in the way the organization operates. A second manifestation encompasses all of the small changes that take place within an organization, on a daily basis, to solve problems and improve processes.
Both types of improvements contribute to fulfilling the requirements of ISO 9001. The key is being able to demonstrate that the improvements were identified and implemented.
How Do We Implement a Comprehensive Continual Improvement Program?
One of the best continual improvement models available today, which meets the requirements of ISO 9001, combines the following:
Team Oriented Problem Solving (TOPS): Uses teams to complete projects identified by the management group (steering committee), which contribute to the attainment of the Quality Objectives.
Lean: Improves the organization’s processes by eliminating the waste - - things the customer is unwilling to pay for.
Six Sigma: Improves the organization’s processes by reducing the variation or inconsistencies in your products and services, which do not meet customer requirements or expectations.
Team Oriented Problem Solving (TOPS)
Steering Committee
The first agenda of TOPS is to establish The Steering Committee, which is made up of upper management individuals that are involved in setting the strategic direction of the company. This group of people is charged with the following responsibilities:
- Schedule and run monthly meetings
- Manage the Project Hopper
- Maintain To-Do Lists for its members (Kaizen Newspaper)
- Evaluate potential projects as to their impact on strategic objectives
- Select projects to fund
- Initiate the project team with a Champion, Team Leader, and Facilitator
- Participate in Monthly Team Status Reports
- Review Final Project Report-Outs
- Communicate Results
- Reward The Teams
Projects
The Steering Committee maintains a Project Hopper of potential projects and prioritizes them based on their impact on the attainment of the organization’s strategic objectives. A project in this continual improvement model follows the
DMAIC project methodology, which has five stages:
- Define: Identify the problem, the voice of the customer and the project goals. Document these in a Project Charter, which becomes the contract between the management group and the project team.
- Measure: Collect information from available data and subject matter experts to gain an in-depth understanding of the key aspects of the current process.
- Analyze: Collect data to determine the root cause through the investigation and verification of cause-and-effect relationships. Determine what factors have the biggest impact.
- Improve: Determine the best combination of factors and implement them in order to achieve the observed improvements in the current process.
- Control: In order to preserve the gains achieved through this Continual Improvement endeavor, controls must be implemented to prevent back-sliding until the new methodology becomes engrained into the culture of the organization.
Teams
The Steering Committee initiates a team for projects, which have been given the go-ahead. Teams consist of the following members or roles:
Champion |
An executive with sufficient authority to provide the necessary resources requested by the team, remove any obstacles, which may hinder or halt the project and assure implementation of team recommendations (not an active team member) |
Team Leader |
The one with the most to gain by solving the problem or completing the project |
Facilitator |
An expert in problem solving methods that will teach and coach the team |
Recorder |
The team member that takes minutes and is responsible for all the team documentation |
Cross-Functional Members |
A team comprised of subject matter experts from various disciplines |
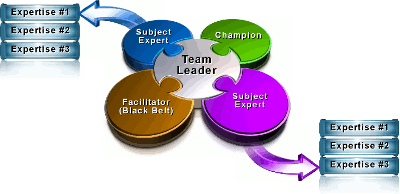
As depicted in this team structure diagram, the subject matter experts bring additional knowledge to the team from their co-workers in the areas in which they work. This is important because the size of the team must be relatively small in order for it to function effectively. Ideally, teams should not have more than five or six full-time members.
Communication
Communication is a critical function of the steering committee.
First of all, the importance of continual improvement must be communicated to everyone in the organization. All employees must understand their role in continual improvement, which starts with an understanding of the concepts, continues with their active participation on a team or as a subject matter expert (one who provides knowledge to the team) and concludes with their support of the new implemented improvements. Without comprehensive employee involvement, active continual improvement will fail.
Secondly, all continual improvement efforts, including all on-going and completed projects, must be communicated and accessible by all employees in order to minimize any threats employees may perceive.
The concepts of Visual Management are a great way to initiate communication. One possibility is a company bulletin board that is seen by all employees, numerous times during the day. A typical bulletin board may contain some of the following items:
- Internal Communication
- Steering Committee Members
- On-Going Projects
- Completed Project Articles
- Project Hopper
- Kaizen Newspaper
- Statement of Commitment From Executive Management
- Mechanism for Submitting Project Ideas
- Lean Six Sigma/Term of the Week
Lean
The Lean part of the continual improvement model provides a number of tools we can use to identify and eliminate waste in our processes. The eight deadly wastes are:
- Inventory
- Over Production
- Over Processing
- Transportation
- Correction
- Waiting
- Motion
- Not utilizing the talent and knowledge of human resources
Most of these wastes are present in our current process and contribute cost to our product or service. Unfortunately, the customer does not want to pay for these costs. If we continue to include them, eventually our customers will go elsewhere.
Some of the tools we have available in our Lean toolbox include:
- Value Stream Mapping (VSM)
- 5S+
- Standard Work
- Setup (Changeover) Reduction
- Total Productive Maintenance (TPM)
- Mistake Proofing
- Continuous Flow
- Kanban
Six Sigma
The Six Sigma part of the continual improvement model provides a number of tools we can use to identify and reduce variation in our processes. Variation is present in our processes due to the influence of:
- People
- Machines
- Materials
- Environment
- Methodologies
- Tooling
Unfortunately, none of these influences can be controlled to the point that they repeat exactly the same way every time. As a result, we have variation. If the variation in our processes becomes excessive, we end up with nonconforming products or services. Since the customer will not tolerate excessive variation, they will not accept our product or service and we will have to redo it, adding cost.
Some of the following tools help us identify, understand, and reduce the variation in our processes:
- Process Mapping
- Control Charts
- Failure Modes and Effects Analysis
- Capability Analysis
- SPC
- Design Of Experiments (DOE)
Back to ISO 9001
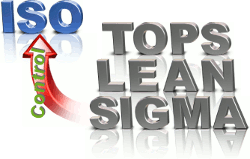
After eliminating the waste and reducing the variation in our processes, we come full circle back to ISO 9001 to help us sustain the gains we have achieved. ISO 9001 and all the other Quality Management System standards provide a number of requirements that, if followed, will lead to improved processes, which will remain improved. Five of these include:
- Document Control: ISO 9001 has a document control process that requires document change notifications, owner and cross functional reviews, controlled distribution, and document training. Any documents generated or revised as part of the continual improvement project can be controlled via ISO 9001.
- Internal Auditing: The whole concept of internal auditing provides a feedback loop to the management group of nonconformances, opportunities for improvement and the current status of a process with respect to the targeted performance measures. Any deviations from expected performance need to be identified during an internal audit.
- Corrective and Preventive Actions: The corrective and preventive action clauses of ISO 9001 require that action be taken whenever deficiencies are identified, which may compromise the integrity of the Quality Management System. This is exactly what we need to do if our new or improved process does not meet expectations in order to prevent back-sliding.
- Process Measurement: The ISO 9001 requirement to monitor processes for effectiveness is a discipline, which will facilitate the measurement of the improved process. Targets need to be established, data collected and analyzed, and results audited and reviewed by management.
- Management Review: The last step in the loop is management review. The management group must periodically review all aspects of the Quality Management System including; performance measures, internal audits, corrective/preventive actions, continual improvement activities, customer satisfaction and customer feedback. Management, those who can authorize the allocation of resources, is constantly in the loop evaluating the information and making decisions to get back on track.
As you can see, ISO 9001 and all the other Quality Management System standards work well with Lean Six Sigma to provide a robust continual improvement process, which meets the requirements of these standards and provides the documented evidence of compliance.