The Akron-Canton Section (#810) of the American Society For Quality held their Spring Quality Conference on April 29, 2011 at the Kent State University Stark Professional Education and Conference Center in North Canton, Ohio. One of the speakers was John Novak, president of KAVON International, Inc. and a Certified Lean Six Sigma Master Black Belt. John spoke on the topic of "Problem Solving".
Problem Solving
John started by creating a number of typical scenarios, which illustrated some concerns relative to problem solving:
- Customers perceive problems when we don’t
- Problems are recurring
- Problems overwhelm us because we don’t know how to identify root causes
- Management doesn’t give us permission to solve problems
John provided some quotes by noted business professionals to illustrate the impact of problems and an organization’s unwillingness to change the way they do business.
Dr. W. Edwards Deming:
"The biggest cost of poor quality is when your customer buys it from someone else because they didn't like yours."
"It is not necessary to change. Survival is not mandatory."
Jack Welch
"When the rate of change outside exceeds the rate of change inside, the end is in sight."
John indicated that in order to solve a problem, we have to know when a problem exists, which he defined as the difference between the current situation and a standard. Without standards, there are no problems.

John went on to emphasize the importance of identifying the problem, as early as possible, in order to minimize the cost of correction.
Next, John compared some of the popular problem solving methodologies:

Plan-Do-Check-Act
PDCA was pioneered by Walter A. Shewhart in the late 1920’s and popularized by W. Edwards Deming in the 1950’s. The entire cycle is repeated over and over for continual improvement. Knowledge is gained during each iteration of the cycle.

8D (Eight Disciplines)
8D was developed by the Ford Motor Company as part of their TOPS (Team Oriented Problem Solving) program. It is very popular in the automotive industry for handling a corrective action request.
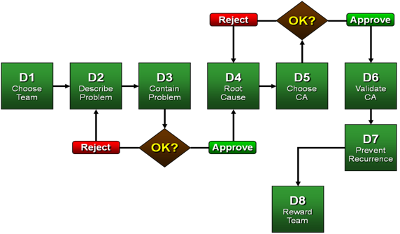
DMAIC (Define, Measure, Analyze, Improve, Control)
The five phase DMAIC roadmap is considered the project management standard used by Six Sigma practitioners.

John focused on the DMAIC problem solving approach and provided detailed insight into each phase.
Finally, John left everyone with this final thought:
"You want continual improvement? Then I challenge every employee in the organization to discard the status quo and ask themselves every day, How can I improve my job?, then find a way to make it happen."